We partner with customers throughout their projects, from design to completion. Our engineers provide expert guidance in selecting the ideal valves for their process, pipeline, and industrial plant.
Design Engineering
- Valve Selection: Fluid Properties: Determine the type of fluid (liquid, gas, slurry), its temperature, pressure, viscosity, corrosivity, and any other relevant characteristics.
- Flow Requirements: Define the desired flow rate, pressure drop, and controllability.
- Application: Consider the specific application (e.g., on/off service, throttling, mixing, isolation).
- Environmental Conditions: Account for factors like ambient temperature, humidity, and potential for vibration or shock.
- Safety and Reliability: Prioritize safety features (e.g., emergency shut-off, fire-safe design) and ensure high reliability to minimize downtime.
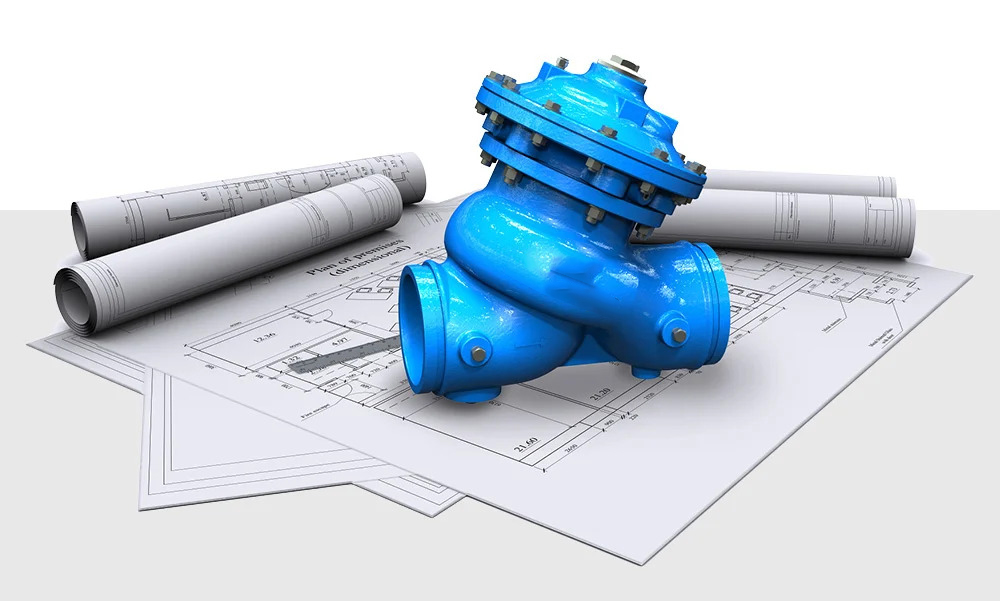
Material Selection:
- Body, Bonnet, and Trim: Choose materials compatible with the fluid and operating conditions (e.g., stainless steel, carbon steel, alloys) to resist corrosion, erosion, and high temperatures.
- Sealing Elements: Select appropriate materials for seals (gaskets, packing, seats) to ensure leak-tight operation and long service life.
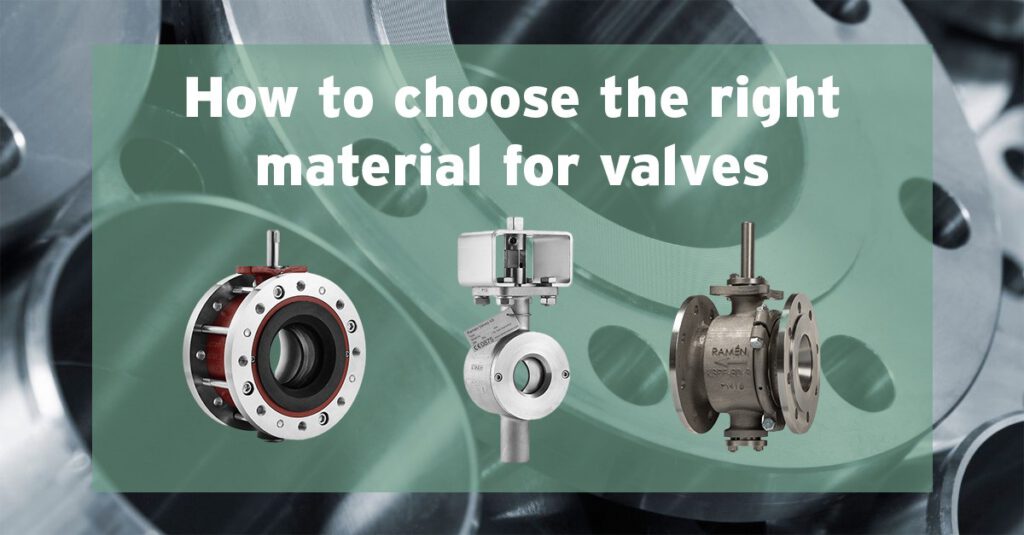
Design Calculations:
- Hydraulic Calculations: Determine pressure drop, flow velocity, and other critical parameters.
- Strength Calculations: Ensure the valve can withstand the operating pressures and temperatures without failure.
- Stress Analysis: Utilize finite element analysis (FEA) to optimize the design and identify potential stress concentrations.
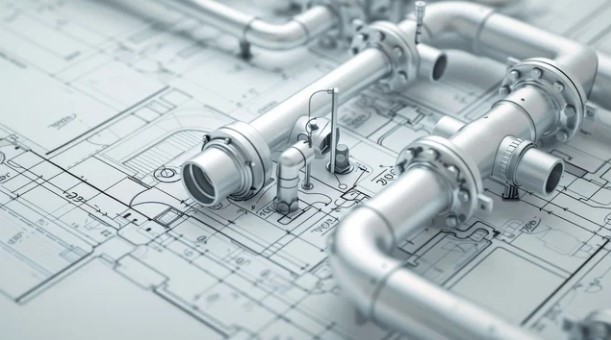
Actuation:
- Manual: Design for easy and safe operation by hand.
- Pneumatic: Utilize compressed air for actuation, providing fast and powerful operation.
- Hydraulic: Employ hydraulic fluid for high force applications.
- Electric: Use electric motors for automated control and integration with control systems.
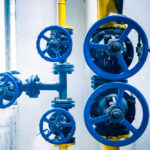
Production Engineering
Manufacturing Processes:
- Casting: Create valve bodies and other components using various casting methods (e.g., sand casting, investment casting).
- Forging: Shape components using forging techniques for enhanced strength and durability.
- Machining: Precisely machine components to achieve tight tolerances and desired geometries.
- Welding: Join components using appropriate welding techniques (e.g., TIG, MIG) to ensure strong and leak-free connections.
- Heat Treatment: Improve material properties through processes like annealing, quenching, and tempering.
- Surface Treatments: Apply coatings (e.g., chrome plating, hardfacing) to enhance corrosion resistance, wear resistance, and lubricity.
Quality Control:
- In-Process Inspection: Conduct rigorous inspections at various stages of production to ensure adherence to design specifications and quality standards.
- Non-Destructive Testing (NDT): Employ techniques like radiography, ultrasonic testing, and magnetic particle testing to detect internal flaws.
- Leak Testing: Perform pressure tests to verify leak-tightness of the valve.
- Performance Testing: Test the valve’s performance under simulated operating conditions to ensure it meets design requirements.
Installation:
- Piping Design: Ensure proper piping design, including pipe size, supports, and isolation valves, to facilitate installation and maintenance.
- Valve Mounting: Install the valve securely and correctly, ensuring proper alignment and support.
- Actuation System Installation: Install and configure the actuation system (e.g., pneumatic cylinders, electric motors) according to the design specifications.
- Instrumentation and Control: Install sensors, transmitters, and control devices (e.g., positioners, limit switches) as required for proper operation and monitoring.
- Testing and Commissioning: Conduct thorough testing of the installed valve to verify proper operation and functionality.
Troubleshooting:
- Identify Symptoms: Observe the valve’s behavior, including leakage, slow operation, noise, vibration, or failure to operate.
- Gather Data: Collect relevant data, such as operating pressure, temperature, flow rate, and any error messages from the control system.
- Analyze Causes: Investigate potential causes of the problem, such as:
- Mechanical issues: Wear and tear, damaged seals, broken parts.
- Hydraulic issues: Cavitation, water hammer, incorrect fluid levels.
- Pneumatic issues: Air leaks, insufficient air pressure, incorrect actuator settings.
- Electrical issues: Wiring problems, faulty sensors, control system malfunctions.
- Implement Corrective Actions: Repair or replace damaged components, adjust settings, and address any underlying issues.
- Preventive Maintenance: Implement a regular maintenance schedule to prevent future problems and ensure the valve’s continued reliable operation.